Cold chain packaging is vital in the pharmaceutical industry, serving as a protective shell for temperature-sensitive products during storage and transport. This packaging type maintains specified temperature ranges, ensuring the safety and effectiveness of these life-saving goods.
Yet beneath those sturdy boxes and containers, hidden magic lies, like insulating materials such as expanded polystyrene or vacuum insulated panels – unsung heroes keeping temperature extremes at bay. These light yet durable materials are key players behind the scenes, safeguarding precious cargo every step of their journey. And this is what you’ll find at Preferred Packaging.
The pharmaceutical industry relies on cold chain packaging to maintain the integrity and efficacy of temperature-sensitive medications and vaccines during storage and transportation. This specialized packaging ensures that products remain within specified temperature ranges, safeguarding patient safety and regulatory compliance.
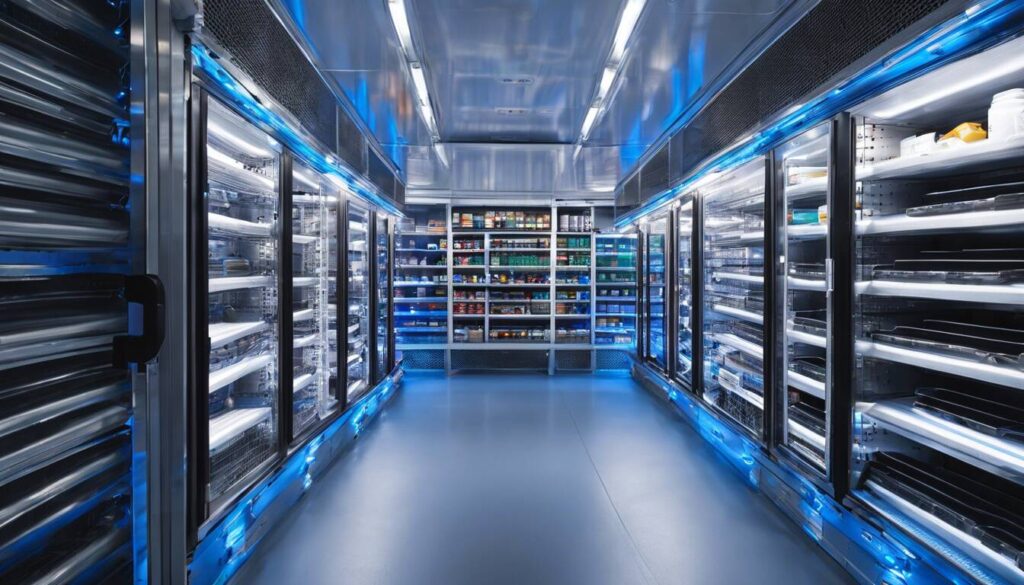
Overview of Cold Chain Packaging in Pharmaceutical Industry
The pharmaceutical industry requires specialized cold chain packaging to preserve the integrity and effectiveness of temperature-sensitive products. These products can be anything from vaccines and biologics to certain medications. To maintain their potency, it’s crucial that these items are stored and transported within specific temperature ranges, as any deviation could compromise their efficacy and safety.
Just like serving food at its ideal temperature ensures the best taste and quality, maintaining the correct temperature for pharmaceutical products guarantees their effectiveness. This is where cold chain packaging steps in. Unlike ordinary packaging materials, cold chain solutions are designed to keep products within critical temperature thresholds during storage and transit. They provide a reliable insulation barrier against external temperature fluctuations, ensuring that the pharmaceuticals inside maintain their efficacy.
For instance, vaccines are highly temperature-sensitive and need to be stored and transported within strict temperature limits to remain effective. Cold chain packaging plays a crucial role in safeguarding these delicate products, helping to prevent spoilage and maintaining their efficacy until they reach the end-user.
At Preferred Packaging, we understand the significance of maintaining product integrity during transportation, which is why we offer a wide range of carefully crafted cold chain packaging solutions specifically tailored to meet the unique needs of the pharmaceutical industry.
Understanding Insulated Material in Cold Chain Packaging
When it comes to protecting pharmaceutical products during transport, the materials used in packaging play an essential role. Expanded polystyrene (EPS) and vacuum insulated panels (VIPs) are two standout materials commonly employed for their exceptional thermal insulation properties.
Expanded Polystyrene (EPS): This lightweight, sturdy material is widely used in cold chain packaging due to its ability to effectively maintain consistent temperatures while safeguarding pharmaceutical products. EPS ensures that the temperature-sensitive medications remain within their specified temperature range throughout the transportation process, thereby preserving their efficacy and safety for patients.
Vacuum Insulated Panels (VIPs): VIPs are another highly effective material for thermal insulation in cold chain packaging. They consist of a core material enclosed within a gas-tight barrier that eliminates air molecules from entering, creating a near-perfect vacuum. This construction allows VIPs to provide superior insulation performance, making them ideal for long-term temperature control during the transit of pharmaceuticals.
Both EPS and VIPs are chosen for their durability and ability to withstand the rigors of shipping. The robust nature of these insulated materials ensures that crucial pharmaceutical products remain well protected from external environmental factors such as extreme temperatures and humidity fluctuations, thus maintaining their integrity and effectiveness upon reaching their destination.
It’s important to note that the use of these thermal insulating materials aligns with the stringent regulatory requirements set forth by health authorities and regulatory bodies governing pharmaceutical transportation. These regulations mandate the maintenance of specific temperature ranges for pharmaceutical products to ensure their safety, efficacy, and compliance with quality standards.
Key Benefits of EPS and VIPs in Cold Chain Packaging
Benefit | Description |
---|---|
Lightweight | Ensures ease of handling and reduced shipping costs |
Durable | Withstands the challenges of shipping without compromising product protection |
Superior Insulation | Maintains consistent temperature conditions during transit |
Compliance with Regulations | Meets stringent industry standards for pharmaceutical transport |
Understanding the critical roles of insulated materials such as EPS and VIPs provides insight into why they are essential components of cold chain packaging processes. These materials serve as reliable guardians, preserving the potency and efficacy of life-saving pharmaceutical products throughout their journey from production to patient care.
Cooling Equipment in Pharma Transportation
When it comes to pharmaceutical transportation, maintaining the temperature of the products within a specific range is crucial. This is where cooling equipment plays a pivotal role. Refrigerated trucks, insulated containers, and portable refrigeration units are fundamental components of this process.
These specialized systems are specifically designed to ensure that pharmaceutical products remain within the required temperature range throughout their journey from the manufacturing facility to their final destination.
Refrigerated trucks are indispensable for the safe delivery of pharmaceuticals, providing a controlled environment to maintain the required temperature. These trucks are equipped with advanced refrigeration systems that can maintain the necessary temperature range even during long-distance transportation. Similarly, insulated containers play a critical role in maintaining the cold chain during shipment. They provide an additional layer of protection to pharmaceutical products, shielding them from external temperature fluctuations and ensuring their integrity.
Apart from refrigerated trucks and insulated containers, portable refrigeration units are also widely used in pharmaceutical transportation. These units offer flexibility and can be employed in various settings, including warehouses, distribution centers, and during transit. Their versatility allows for maintaining the required temperature at different stages of the supply chain, thereby safeguarding the efficacy and safety of pharmaceutical products.
For instance, if a batch of temperature-sensitive vaccines needs to be transported from a manufacturing facility to a healthcare provider or distribution center, refrigerated trucks will play a pivotal role in ensuring that the vaccines remain within the recommended temperature range. The use of insulated containers further reinforces this protection, especially during transshipment or temporary storage.
In conclusion, these essential cooling equipment options—refrigerated trucks, insulated containers, and portable refrigeration units—serve as critical components in pharmaceutical transportation. Their primary function is to secure the integrity and potency of pharmaceutical products by maintaining optimal temperature conditions throughout their journey. Choosing the right cooling equipment tailored for pharmaceutical transportation needs is essential for ensuring product safety and effectiveness.
The Debate: Active versus Passive Systems
In the sphere of transporting temperature-sensitive pharmaceutical products, the debate between active and passive cold chain systems is crucial. Active systems, utilizing mechanical cooling mechanisms, provide precision temperature control throughout the entire journey, akin to your car’s air conditioning keeping things at the optimal temperature no matter what’s happening outside.
On the flip side, passive systems forgo mechanical cooling and rely on advanced insulation materials and phase change materials to maintain the required temperature—a bit like packing an ice chest for a picnic and hoping the ice holds out until you reach your destination.
Advantages of Active Systems:
- Precision Control: Offers precise temperature control, ensuring that pharmaceutical products remain within their required temperature range.
- Real-Time Monitoring: Equipped with sensors and monitoring devices to constantly track and adjust temperatures as needed.
- Reliability: Mechanical nature means they can reliably maintain desired temperatures, even in extreme ambient conditions.
Moving on to the advantages of passive systems:
Advantages of Passive Systems:
- Cost-Effective: Usually more economical than active systems as they don’t require power sources or mechanical components.
- Environmentally Friendly: Lower environmental impact due to no reliance on power sources, making them a greener solution.
- Simplicity: Easier to transport and implement without the need for mechanical parts or power.
The decision between active and passive cold chain systems ultimately depends on various factors such as budget, transportation distance, and specific pharmaceutical product requirements. Each option carries its own set of advantages and limitations.
It’s crucial to carefully consider the specific needs of each pharmaceutical product before choosing an appropriate cold chain system. For instance, highly sensitive biological products might benefit from the precise control offered by active systems, while less critical products could be comfortably transported using cost-effective passive solutions.
Understanding the nuances of both these options is vital for ensuring the safe and effective transport of pharmaceutical products across different environmental conditions and transportation durations.
As we’ve unraveled the complexities surrounding active and passive cold chain systems in pharmaceutical transportation, it’s time to shift our focus towards ensuring that these sophisticated systems are maintained optimally under varying circumstances.
Maintenance of Cold Chain Conditions
When preserving the integrity of pharmaceutical products during transit, maintaining the cold chain conditions is paramount. It involves more than just packing products into a cooler – it requires ongoing diligence, attention to detail, and adherence to strict protocols.
Rigorous temperature monitoring plays a crucial role in maintaining the cold chain. This involves using advanced technology such as data loggers and temperature sensors to continuously monitor environmental conditions throughout transportation. These monitoring devices provide real-time data, alerting parties involved if the temperature deviates from prescribed ranges. Immediate corrective action can then be taken to prevent any damage to pharmaceutical products.
Adhering to standard operating procedures (SOPs) is essential in ensuring that every step of the distribution process aligns with industry best practices. SOPs outline specific guidelines for handling, storage, and transport of pharmaceutical products within the cold chain, serving as a blueprint for logistics personnel. This ensures that each stage is executed precisely as required to maintain the desired temperature conditions.
Regular maintenance of cooling equipment is a fundamental aspect of preserving cold chain conditions. Equipment such as refrigerated trucks and storage units must undergo routine checks and maintenance to guarantee optimal functionality. Any malfunctions or inefficiencies can lead to deviations in temperature, posing risk to the quality and efficacy of pharmaceutical products.
Proactive measures must be in place to address potential equipment failures, including backup systems and redundancy plans. These contingency plans ensure that even if primary cooling equipment encounters an issue during transit, alternative mechanisms can maintain necessary temperature conditions for pharmaceutical products.
Overall, meticulous attention to temperature monitoring, strict adherence to SOPs, and regular maintenance of cooling equipment are essential components in upholding cold chain conditions for pharmaceutical products. By implementing these measures, pharmaceutical companies can safeguard the quality and efficacy of their products throughout the entire distribution process, ultimately benefitting patients who rely on these vital medications.
Safeguarding Pharmaceuticals during Storage and Transport
The pharmaceutical sector recognizes the paramount importance of preserving the integrity and safety of its products throughout every stage of the process. When it concerns transport and storage, the utilization of cold chain packaging assumes a critical role in ensuring the safe passage of these products.
Cold chain packaging integrates several protective features designed to safeguard pharmaceutical items. One such feature is the tamper-evident seal, offering visual cues if the product has been tampered with. This not only enhances security but also assures that the medication inside remains uncontaminated and undisturbed.
Additionally, cold chain packaging incorporates shock-absorbing materials to shield pharmaceutical products from physical harm during transit. These materials act as a barrier against external forces, such as bumps or drops, which could potentially compromise the quality of the medications.
Secure closures represent another essential component of cold chain packaging, providing airtight and secure seals to prevent unauthorized access to pharmaceutical products. By doing so, they maintain the integrity of the medications throughout their journey.
For instance, consider a delicate vial or syringe containing a life-saving vaccine. Without the protective measures provided by cold chain packaging, these pharmaceutical products would be vulnerable to contamination, physical damage, or unauthorized access. Cold chain packaging acts as a shield, ensuring the safety of these critical medications at every turn.
By implementing these measures in cold chain packaging, the pharmaceutical industry can confidently assert its fulfillment of ensuring pharmaceutical products reach patients in a safe and effective condition. The protection afforded by features such as tamper-evident seals, shock-absorbing materials, and secure closures is essential in upholding the safety and integrity of pharmaceuticals during storage and transport.
In this conscientious practice of ensuring product safety lies an intricate web of exacting standards and meticulous monitoring that defines quality assurance within the cold chain.
Ensuring Quality within the Cold Chain
Ensuring quality within the cold chain is a meticulous process. At every step, from manufacturing to delivery, adhering to specific guidelines and measures is vital to maintain the integrity and efficacy of pharmaceutical products.
Furthermore, traceability measures play a crucial role in maintaining quality within the cold chain. Implementing systems that allow for tracking and tracing pharmaceutical products at every distribution stage is essential. By doing so, any issues or discrepancies can be promptly identified and rectified, ensuring that only high-quality, uncompromised products reach patients.
Advanced technologies such as barcode scanning and RFID (Radio-Frequency Identification) systems enable real-time tracking of pharmaceutical shipments, providing valuable insights into product location, temperature conditions, and transit times.
Adherence to guidelines, regular audits, and robust traceability measures are essential components in ensuring the high-quality standard of pharmaceutical products within the cold chain. These measures not only uphold the safety and effectiveness of medicinal products but also build trust among healthcare providers and patients alike.
In a delicate ecosystem like the pharmaceutical industry, upholding stringent standards isn’t just about compliance—it’s about safeguarding patient health. By prioritizing quality assurance measures within the cold chain, pharmaceutical companies play an indispensable role in ensuring that essential medications reach those who need them most.
